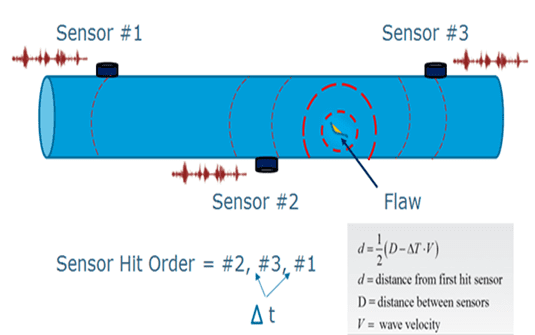
Acoustic Emissions (AE) is a highly underused Non Destructive Testing (NDT) method in Western Australia.
For decades this technology has been used in Offshore Oil rigs, Aerospace facilities and other industries but it has not penetrated the Australian market as well as it has overseas. This is mostly due to a lack of knowledge both of its possible uses and reliable application by NDT companies.
4 years ago Rapallo gained the valuable experience of an AE specialist. Building on a first few tentative projects, Rapallo have since used AE on several projects. Saving, in some cases, our clients millions of dollars in Inspection and maintenance. Below is a brief explanation of Acoustic Emissions, its possible applications and some Case Studies on Rapallo’s successful application of this exceptional technology.
Acoustic Emissions Testing – Non Destructive Testing (NDT)
Acoustic Emissions (AE) testing is a method for examining behavior of materials deforming under stress. Basically – like many people, when materials are under stress they talk. With Acoustic Emissions testing or monitoring, you can “listen” to the sounds of cracks growing, fibres breaking and many other modes of active damage in stressed materials.
The Acoustic Emission Non Destructive Testing (NDT) technique is based on the detection and conversion of high frequency elastic waves into electrical signals. This is accomplished by directly coupling piezoelectric transducers on the surface of the structure while under test and loading.
Sensors are coupled to the structure, and the output of each sensor (during structure loading) is amplified through a low-noise preamplifier, filtered to remove any extraneous noise and furthered processed by suitable electronic equipment.
Benefits of Using Acoustic Emission (AE) testing
• Shut down is not required. Plant remains in normal operation. Natural operational cycle provides the dynamic load
• Removes the need for confined space entry which reduces the risk to personnel health and safety
• 100% Structural Integrity survey of the complete shell compared to partial examination by traditional NDT methods, including visual inspection. Detecting crack initiation, growth and location. A crack only needs to propagate by 100 – 200 μm in ferrous material in order to generate the burst of energy large enough for detection.
• Potential to extend the interval between shutdown inspections as per AS 3788
• Risk mitigation by periodic or continuous condition monitoring
• Full removal of cladding and insulation is not required
• Improved awareness of the shell integrity, early warning of potential integrity issues
• Targeted repairs and preventative maintenance directed to specific locations that otherwise will not be known
With Acoustic Emissions testing small-scale damage is detectable long before failure, saving you time, money and minimising risk to safety.
Where is Acoustic Emissions (AE) used?
• Pressure equipment: This technique has become a reliable and standard method of Non Destructive Testing (NDT) for pressure vessels. Acoustic Emissions (AE) is used to monitor flaws, corrosion and leakage in pressure vessels, LPG tanks, piping systems including transmission pipes and steam generators
• Petrochemical and chemical: storage tanks, reactor vessels, offshore & onshore platforms, drill pipe and pipelines
• Civil engineering: bridges, dams, suspension cable bridges, concrete structure reinforced by steel and composite
• Aircraft and aerospace: aerospace structures, wings, fuselages, bulkheads, fuel tanks, rocket engines, turbine engines
• Maritime: ship hulls and superstructure, tanks, cranes and derricks, engine and power plants
• R&D: to monitor and study the damage in materials and their mechanical properties. R&D in the control of the damage in materials has grown in the last 20 years.
Rapallo is an experienced user of Acoustic Emissions testing to optimise the performance of our clients assets from LNG plant to tanks and smelters.
Rapallo Acoustic Emissions Case Study 1 – LNG Processing Plant
Objectives
1. Gather sufficient data to inform the pressure vessel inspector’s decision process on Fitness For Service (FFS) for each vessel (Amine Contactor and Amine Still)
2. Quickly identify any anomalies from the Acoustic Emissions that might need to be addressed in the shutdown
3. Characterise transient loads produced by the shutdown and start up procedures
4. Establish a baseline of AE data mapped to each vessel from which trends can be determined from future Condition Monitoring
5. Provide a Condition Monitoring report on the internal fittings and fixtures
Benefit to Client
• Improved safety – confined space entry negated
• In-service – no shutdown required
• Planned shutdown subsequently de-scoped
• Significant cost savings utilising Rapallo’s “one-stop shop” service
• On-going compliance management support
• Intrinsically safe (ATEX approved) Condition Monitoring equipment
Rapallo Acoustic Emissions Case Study 2 – Smelting Facility
High Temperature Pipeline with AE sensor installed on a Wave guide
Problem
• Ageing saturated steam pipes
• Never previously inspected
Solution
• In-service Condition Monitoring (CM) using Acoustic Emissions (AE) along with complimenting Non Destructive Testing (NDT)
Benefit to Client
• De-scoped from shutdown
• No requirement for total de-lag
• Facilitate Condition Based Maintenance (CBM)
Rapallo Acoustic Emissions Case Study 3 – High Risk Smelting Facility
Installing Sensors at a High Risk Smelting Facility
Problem
• Strong acid tank
• High risk to personnel (26 lives at risk)
• Known crack at top of tank
• New tank – Litigation
• Replacement lead time 18 months
Solution
• Conventional Non Destructive Testing (NDT)
• Remote monitoring using Acoustic Emissions (AE)
Benefit to Client
• Characterised crack growth
• Determined cause
• Predicted mode of failure / location
Rapallo Acoustic Emissions Case Study 4 – Smelting Facility
Smelting Facility vessel with Cladding and Lagging
Problem
• Classified Plant omitted from shutdown schedule
• Internal visual inspection – High risk to Health and Safety
• Limited visibility
Solution
• In-service Condition Monitoring (CM) using Acoustic Emissions (AE) with supporting Non Destructive Testing (NDT)
Benefit to the Client
• De-scope shutdown
• Improved inspection / safety
• Saving of $12-16 Million