Slurry feed hoppers are typically used in processing plants to collect slurry mixtures and distribute them to single or multiple outlets that can be connected to pumps or other equipment for downstream processing. If a slurry feed hopper is not designed correctly the solids in the slurry can settle out, build up and restrict the flow out of the hopper causing reductions in plant output and other problems. Issues can also arise if air is entrained into the slurry near the hopper outflow and then enters the pump suction, causing a loss of pump performance.
Recommended hopper design
To prevent slurry settling out in the feed hopper the following guidelines are recommended:
- The height of the hopper must be sufficient to provide an adequate reserve for inflow surges.
- The sump volume of the hopper should be as small as possible to maximise the movement of the slurry while traveling through the hopper. The volume should be based on the slurry retention time. A typical guideline is as short as 15 seconds retention for coarse particles, and up to 120 seconds for fine particles.
- The bottom of the hopper should be sloped at a minimum of 30° and up to 45°, to hinder the accumulation of settled solids.
- The outlet pipe at the base of the sump should be angled at a minimum of 30° towards the ground to allow air in the suction pipe to escape before entering the pipe and to also promote the flow of the slurry out of the hopper.
- The liquid surface area at the free liquid level must be sufficient to allow a continuous release of entrained air or froth.
- The discharge pipe should incorporate a scuttle plug or dump valve in order to drain the pump and the hopper sump.
- Depending on the flow characteristics, the hopper inflow feed should be below the liquid surface to avoid air entrainment, or there should be an angled baffle to aid the escape of air from the slurry. This is especially important with frothy slurries and/or when the inflow is in close proximity to the outflow point.
- The overall hopper geometry should be tall and converging towards the hopper outlet points.
- The slurry should enter at the top of the hopper and the only path of travel for the slurry should be towards and converging point at the bottom outlet points. This minimises stagnant areas in the hoper where the slurry could settle out.
- There should be a reasonable amount of turbulence in the hopper to prevent solids settling out, but not so much that air is entrained into the slurry or excessive turbulence is experienced at the pump suction.
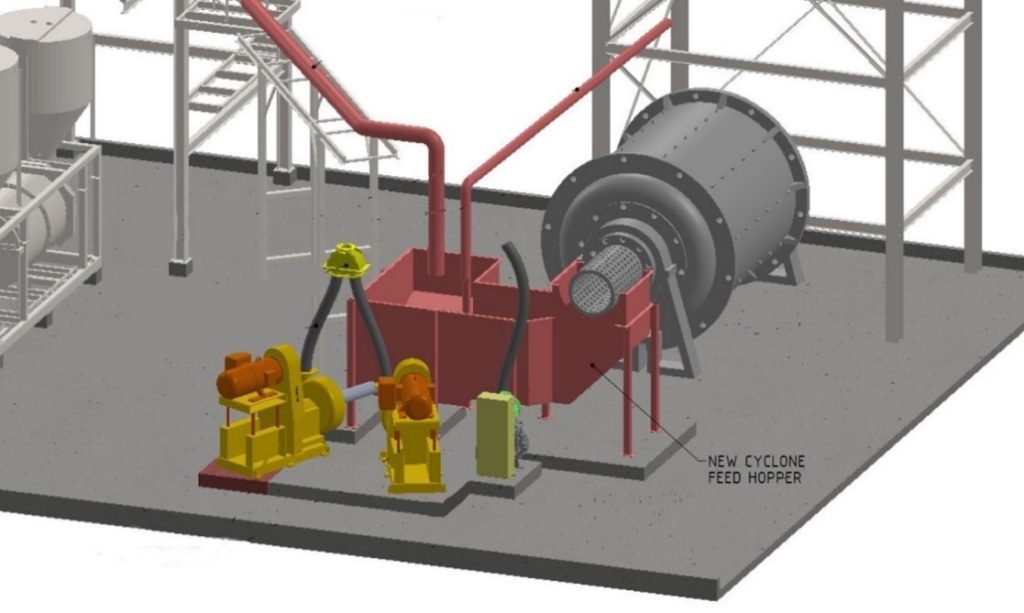
Rapallo Capability
Rapallo has the experience and capabilities to complete new slurry feed hopper designs or assess your existing hoppers and recommend improvements to increase performance. Rapallo has the capability to manage the work from the design stage though to fabrication and construction on site. For more details of Rapallo’s capability visit our website at Engineering & Projects | rapallo.com.au.